In partnership with:: TATA STEEL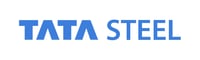
Pre-finished steel has become one of the most popular building envelope solutions worldwide, thanks to the array of design advantages and maintenance benefits it can deliver throughout the whole lifespan of a building. Dr Peter Barker, Manager New Product Development at Tata Steel, explains some of the considerations when specifying pre-finished steel products.
From the day a project is built, to the end of its life-span, the building will be exposed to a variety of challenging environmental conditions. Pre-finished steel is a vastly popular building material, both for commercial and industrial projects, as well as public sector buildings and high-end aesthetic developments, often selected for its colour choice and cladding design options. However, it can also present building owners with a unique set of areas to consider, especially regarding how to ensure the long-term performance of the building.
The durability and longevity of a building is in fact often determined at the specification stage of a project, long before construction has even begun, with decisions often having a huge impact on a structure’s durability and length of life.
Installing a cladding system, which is manufactured from a high quality pre-finished steel is one way in which specifiers can help ensure long-term performance for their building. Suitable for an extensive range of roof and wall construction applications, from composite panels to site assembled systems and rainscreens, pre-finished steel products provide a functional performance and an aesthetically pleasing design.
Pre-finished steel comprises a number of paint layers and treatments that are applied to the steel in an automated and carefully controlled process. Each layer has a particular function and the synergistic effect of these various layers ensures a material that is robust, versatile and aesthetically pleasing.
Part of the manufacturing process of pre-finished steel involves galvanising, where a protective zinc coating is applied to the metal, providing a robust defensive layer and protecting the steel beneath from corrosion. This metallic coating is essential to the performance of the pre-finished steel. Traditionally pre-finished steel products have used a zinc metallic coating which is often referred to as Hot Dipped Galvanised steel however there are also specially developed metallic coatings that provide the best combination of zinc and other elements to offer a combination of increased barrier and sacrificial protection.
Not all pre-finished steel products have the same performance level; like many materials, there are a number of factors that can affect the performance with UV solar radiation and weather conditions being the most detrimental.
Exposure to UV solar radiation can cause a deterioration of colour and gloss, both of which are precursors of paint cracking and delamination, and various weather conditions can contribute to the corrosion of the material itself.
With many pre-finished steel products available on the market, European Standards have put ratings into place to help specifiers understand how the product will perform when exposed to these factors.
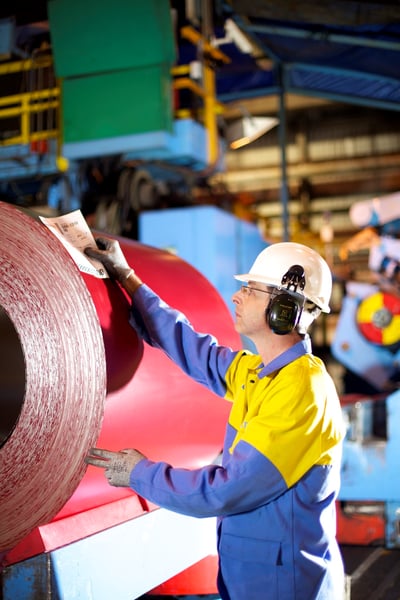
For UV solar radiation, coil coating standard EN 10169 classifies the UV resistance of pre-finished steel from Ruv2 to Ruv4, with the latter being the most demanding. To meet the requirements of Ruv4, the European Standard stipulates that product samples must be exposed to artificial UVA radiation for a total of 2,000 hours and spend two years at an accredited weathering site, with a cumulative UV radiation in excess of 4,500 MJ/m2 per year. Following this rigorous testing process and to achieve the Ruv4 classification, the percentage gloss retention (% GR) must be greater than 80% after each test and the extent of colour change (DE) must be less than 2DE for artificial UV testing and less than 3DE for natural weathering exposure.
In addition to UV solar radiation, EN 10169 also classifies the corrosion resistance of pre-finished steel using the ratings RC1 to RC5. To achieve the highest classification possible, RC5, the pre-finished steel must be subjected to extensive natural weathering tests. For example, samples need to spend more than two years at an extreme coastal location, certified as a C5 environment, and during this time, they must be able to resist blistering, surface damage and edge peel in order to achieve the RC5 classification.
Pre-finished steel products that are classified as RC5 mean that they are suitable for all external environments, from rural and urban to industrial, marine/coastal and sea fronts all of which endure very different conditions.
The corrosive environment classification of an area, including marine/coastal areas, is based on standard ISO12944-2 and ISO 9223, which outlines the ranking of an environment’s corrosiveness, based on a controlled test that measures a given materials mass loss due to corrosion after a 12-month period. This central standard test provides the basis of EN 10169 to classify an external environment from C1 to C5 based on the corrosive, polluting and saline (saltiness) factors present. When specifying a product, it is essential that the material selected has an RC classification suitable for the area’s environment (C1-C5).
Despite Ruv and RC ratings highlighting the performance of different factors, they should not be considered in isolation and instead, specifiers should look at choosing products that have both a high corrosion and UV resistance, Further to this, it’s important to also consider product guarantees that may vary depending on the building’s environmental classification as well as location of the building.
There are certainly products available on the market that are classified as both RC5 and Ruv4. Most pre-finished steel products are typically “2 layers” consisting of a primer and a top coat however one of the latest generations of pre-finished steel, from Tata Steel, includes cutting edge three-layer technology. This innovative multi-coat technology of Colorcoat Prisma® which is produced in one manufacturing run provides superior ultraviolet (UV) resistance and corrosion protection to maintain the colour and long-term aesthetic appearance of the product.
The high build three-layer product is made up with a corrosion resistant primer, before a coloured layer is then applied on top to provide the product’s desired aesthetic finish and the final layer is an additional protective clear layer, which provides an additional barrier to enhance UV resistance. Colorcoat Prisma® pushes the boundaries of UV performance and also surpasses the highest European standards for corrosion resistance.
Incorporating Tata Steel’s corrosion protection experience, the steel is prepared for the three layer process with a Galvalloy® metallic coating consisting of 95% Zinc and 5% Aluminium, which is applied to the base steel substrate before a pre-treatment layer is added. This optimised mix of Zinc and Aluminium, Galvalloy® forms a sacrificial protective layer to provide unrivalled corrosion protection even at cut edges.
Colorcoat Prisma® is the most independently tested product in the 50-year history of Tata Steel’s pre-finished steel products, and has been tested to various standards and certified by a multitude of external bodies such as the British Board of Agrément, Polish ITB, German U-Mark, Russian GOST standards and American Society for Testing and Materials (ASTM).
With the above in mind, when it comes to choosing pre-finished steel building envelope products, it is vital that the performance of the product is taken fully into consideration, to ensure that the end client will receive a building envelope that is not only aesthetically pleasing, but they can rest assured that it will remain looking ‘good as new’ for years to come whilst reducing the need for costly maintenance and replacements in the building’s lifespan.
For more information please visit: www.colorcoat-online.com
Colorcoat, Colorcoat Prisma and Galvalloy are trademarks of Tata Steel UK Limited
Isopan is constantly improving for quality and innovation in its solutions, which is why the partnership using Colorcoat Prisma® and Colorcoat HPS200 Ultra® pre-finished steel from Tata Steel ensures exceptional performance and resistance against corrosion for building envelope applications.
Colorcoat HPS200 Ultra® can be used for roofing products such as ISOCOP, ISOFIRE ROOF and ISOFIRE ROOF FONO. The Confidex® Guarantee which is direct from Tata Steel to the building owner for Colorcoat HPS200 Ultra® ensures the integrity of the product for up to 30 years for the weatherside of industrial and commercial buildings.
Colorcoat Prisma® is a perfect solution for facade applications used in systems with either a PIR core (ISOPARETE, ISOBOX and ISOFROZEN) or mineral wool insulation (ISOFIRE WALL, ISOFIRE WALL FONO and ISOFIRE WALL PLISSE'). Another advantage of Colorcoat Prisma® is the Confidex® Guarantee, which guarantees the pre-finished steel product for up to 30 years.