In collaboration with: ROCKWOOL
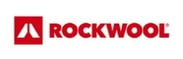
Architects and urban planners face the challenge of designing cities to accommodate a growing population. At the same time, they need to reduce the impact on climate change and withstand increasingly extreme weather conditions. Daniela Pasquero PhD, Engineer and Product Manager at ROCKWOOL Core Solutions explains how stone wool insulated sandwich panels can help.
By 2050, the United Nations estimates that the world’s population will be 11.2 billion and more than two-thirds of people will live and work in urban areas. This will require large-scale development of cities, as well as a radical rethink of building technology.
Globally, today’s buildings account for one fifth of CO2 emissions and one third of operational energy consumption. These figures are even higher in Europe due to the CO2 emissions embedded in materials and the demand from heating, ventilation and air conditioning (HVAC), lighting and water supply systems.
To meet growing demand and future-proof our cities, the construction industry is focusing on carbon footprint during both new-build and renovation projects.
In addition, it needs to apply the concept of circularity to minimize use of resources, cut costs and reduce waste.
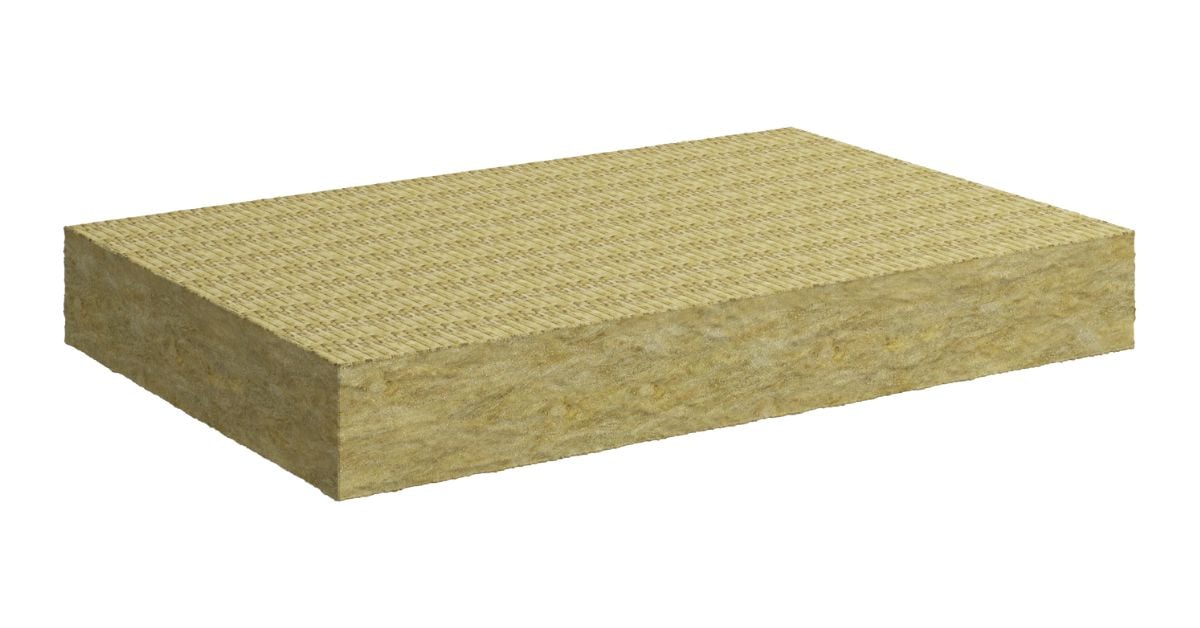
Performance comes first
When it comes to specifying materials for sustainability, building performance always needs to come first. Buildings also need to stand the test of time to make the most of the investment in the energy and materials that is required to build them.
However, the industry needs new materials with the right level of performance, as well as lower environmental footprint. This can be achieved by using recycled materials and low-emission energy sources.
One example is the ROCKWOOL LC Spanrock product (Low-Carbon Spanrock), a new breed of stone wool insulation board designed as the core for sandwich panels. This low-carbon material provides identical performance to the original Spanrock. It is non-combustible and has the same thermal, acoustic and mechanical properties. This means it can provide safety, comfort and flexibility for a building to adapt to new and changing uses over a long life of 80 years or more. In addition, as part of a pre-fabricated sandwich panel system, the insulation will help the construction industry boost the scale and speed of construction while providing an aesthetically-pleasing finish.
Its advantage is that it has 60% lower CO2 emissions than a standard product. Once the insulation is combined with sheet metal into a sandwich panel, the resulting product’s Global Warming Potential (GWP) is 25% lower than one with a standard stone wool core. This small carbon footprint is possible thanks to new developments in stone wool production.
Stone wool is produced by sourcing abundant basalt rock from sources close to our mills and melting it along with upcycled slag from steel production. This molten mix is passed through a spinning device to create fine threads that are formed into insulation. Traditionally, the process used virgin raw materials, heated by burning fossil fuels in a furnace. At ROCKWOOL we are shifting to a low-carbon approach by converting our plants to electric furnaces.
This significantly reduces the CO2 emissions from our process, which are known as Scope 1 emissions under the ISO 14040 environmental management standard.
Sourcing electricity from renewable sources also drives down CO2 emissions under Scope 2.
Upcycling scrap stone wool and waste slag from steelmaking as feedstock for our furnaces limits our Scope 3 emissions. In addition, at the end of its life, the stone wool insulation can be collected and recycled indefinitely.
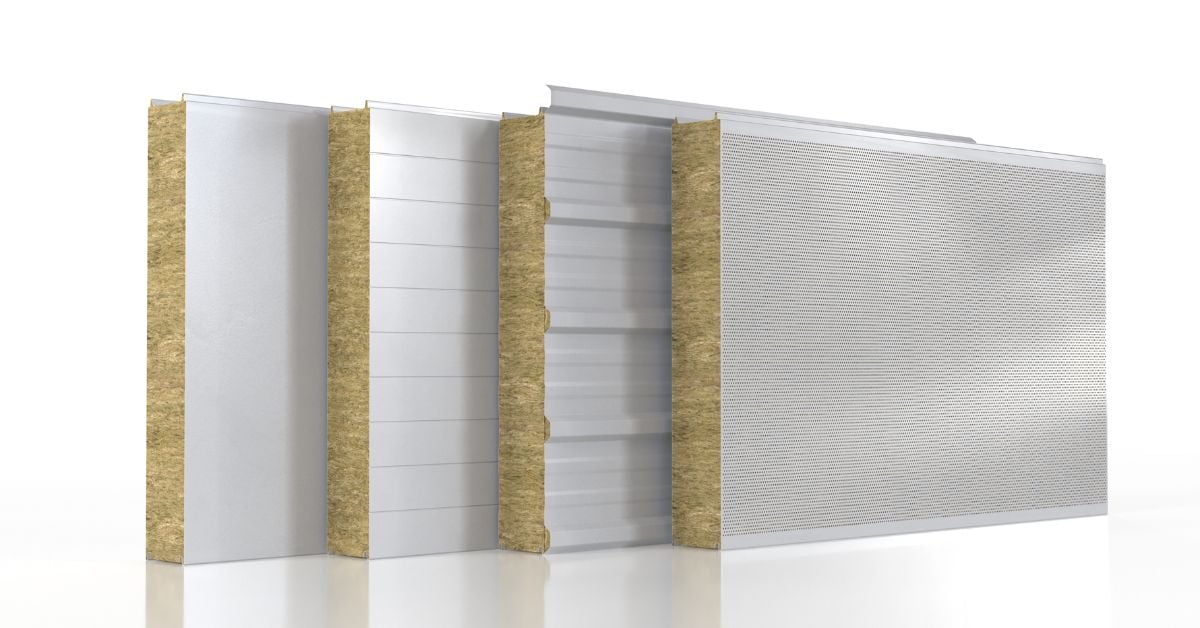
Enabling architects to make informed decisions
While this is positive news, architects and developers also need to understand how the new materials can influence the overall carbon footprint of their building projects. Therefore, we have published a set of environmental product declarations (EPDs) that includes independently verified data on the carbon footprint of our insulation board.
Sandwich panel manufacturers like Isopan, part of Manni Group, can use our data in their own EPDs, along with data from suppliers of steel or aluminum sheet, adhesives.
They can further reduce their carbon footprint by returning offcuts to our mill as stone wool is infinitely recyclable.
The ultimate goal is to provide architects with the tools they need to take informed decisions on the embedded carbon dioxide in building materials and support them in their drive to engage in sustainable building schemes such as BREEAM, LEED, HQE or DGNB.
At ROCKWOOL, we understand that we are part of the supply chain for buildings and that we have an important role to play in helping architects decarbonize the cities of the future. We believe that by decarbonizing our business and value chain, we can reinforce the fact that we’re a net carbon negative company as our products conserve 100 time more energy in their lifetime than they use to make. And we see the next step as providing tools to help our customers decarbonize their own projects.